5 Challenges of Material Sampling in the AEC Industry
- Rajvardhan Agarwal
- Dec 28, 2021
- 3 min read
Updated: Jan 12, 2022
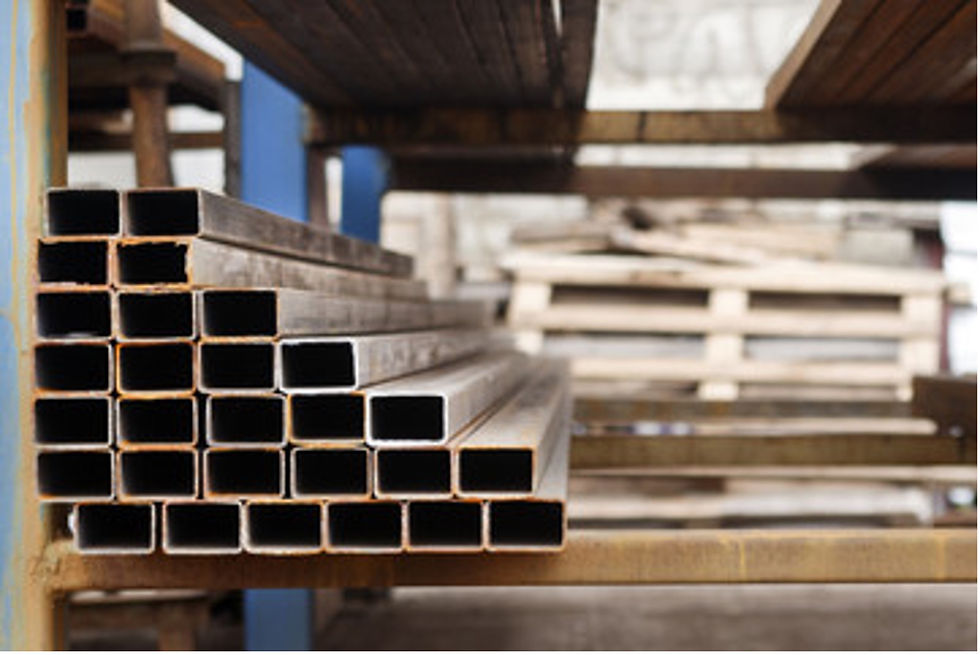
The process of building material selection is an overwhelming one. While some architects are fascinated by the materials like a kid in the candy store, others seem to go through an anxiety rush. Nonetheless, shopping for building materials is an elaborate task that involves many layers. An architect or interior designer needs to consider various factors while finalizing the building materials.
Identifying the material suitability and strength are prime concerns during the selection process. And to cater to these concerns, architects and interior designers resort to material sampling as a viable solution. This activity involves ordering a few materials to assess their correctness for the project.
It not only saves money but also saves time and energy to re-order another set of material or architectural products. But along with these benefits, sampling also comes with its own set of challenges:
1. Manifold Co-ordination Involved
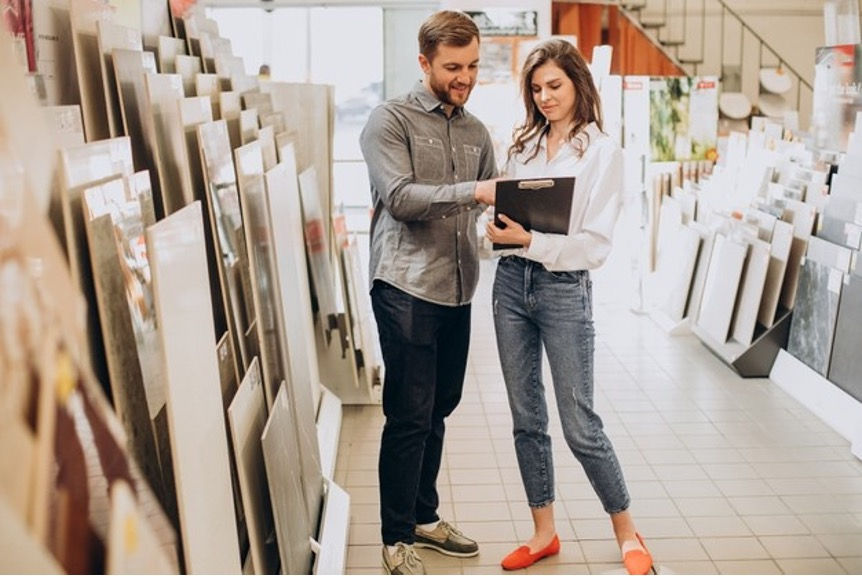
The process of material selection can be tedious as it involves many stakeholders, including the designer, manufacturers, consultants, and the client. It’s crucial for every decision-maker to establish a common ground about their preferences. Material sampling helps the client reach a conclusion about the final product to be used, thereby increasing their satisfaction level. But when so many parties are involved, you can always expect back-and-forth communication about the best-suited materials. This results in a commotion until the sample order is placed and makes client-dealing difficult.
2. An Additional Cost in the Project BOQ

There is no such thing touted as free in the Architecture, Engineering, and Construction (AEC) domain. Although not all sampling materials are chargeable, the customized and imported ones are charged for. The client has to buy the materials and architecture products used for sampling. Hence, considering the cost of these samples in the project estimation is important. It significantly increases the costs mentioned in the project Bill of Quantities (BOQ). Besides, the more customizable and expensive samples a client wants, the more the cost surges.
3. Unused Samples Cannot Be Returned

As mentioned earlier, the materials for sampling have to be bought from the market with a no-return policy. This means that if any material goes unused, you still can’t return it to the vendor. Once the sample has been picked or delivered, they are at the architect’s or interior designer’s disposal. While there are certain vendors who do accept unused samples, they do not give a refund to the buyer. Thus, money once invested into material sampling cannot be retrieved.
4. Limited Scope to Sample From Various Brands
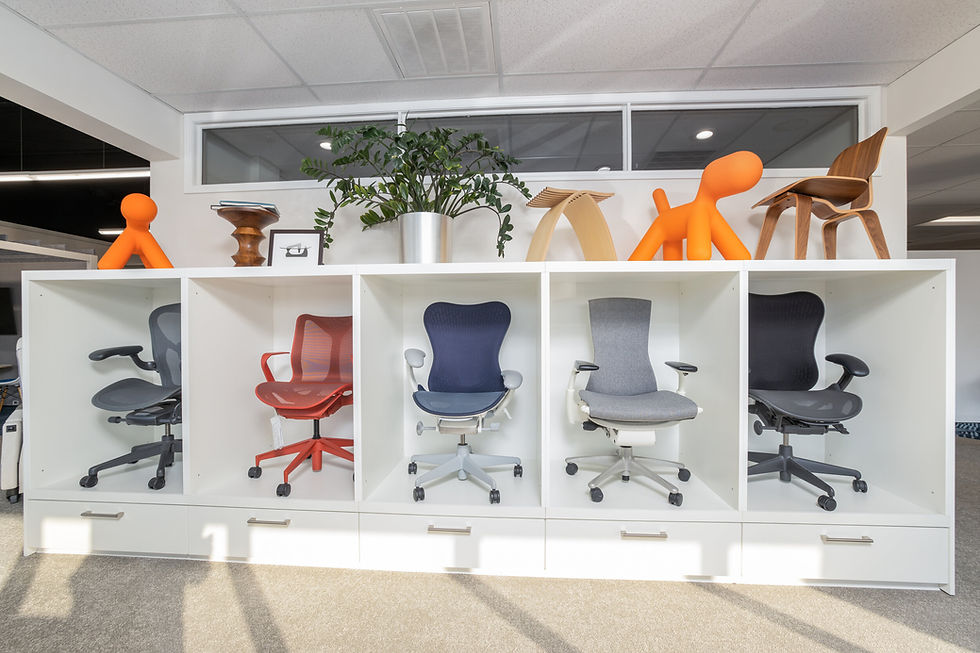
Another challenge in the traditional material sampling process is that when shopping for materials, vendors offer less scope to order materials across multiple brands. The architect has to settle for 2-3 brands to source the samples and experiment with them. It restricts them from exploring more options and limits their creative flow. If an architect has to source more samples, they have to do more frequent site visits. This is primarily important to build connections with vendors so that they do you a favor of providing more architectural product samples. This activity consumes a lot of time and effort, which can otherwise be invested in other design works. But thanks to digitization, things are evolving. Today, there are various online marketplaces that allow you to access product samples from different companies on a single platform.
5. Wrong Materials Delivered

Since many people are involved in material selection, there is a high possibility of wrong materials being delivered on-site. Such mishaps are caused due to a lack of communication. Having the wrong materials delivered on-site fuels the project completion stress. For starters, it delays the project by causing conflicts between the client and the architect. And if you try to return these material samples, there is a huge possibility that the vendor might not take them back. More so, if these materials are mishandled or compromised in transit, the process of return and re-ordering becomes a challenge.
Final Thoughts
With all these concerns to cater to, material sampling is drastically evolving. People are shifting to digital mediums to make the activity hassle-free and transparent. Many online portals such as Archmozzo are bridging the gap towards a user-friendly sampling process. The contemporary architects and interior designers are bringing a shift in sampling by welcoming the digital approach. If you have faced any of these challenges in the traditional material sampling, let us know. And, if you have something more to add to these, drop them in the comments below. We will be glad to have a thoughtful dialogue with you.
Comments